I’m Stephanie, the women behind the New Zealand nursing pillow brand BabyBaby. I’m a mum, a wife, designer, pattern maker and sewer. Seriously, you would think that would keep me busy, and it does believe me, but I’ve always been interested in textile art and surface printing. I just love the perfect imperfections of hand-printed pieces and I wanted in on that action.
So a few years ago, I decided I was going to start screen printing my own fabric, and at the time it didn’t really seem like it was going to be a daunting task. I mean it’s a pretty straight forward process, right? All I had to do was watch some videos, and by some I mean a lot, then create some imagery. I’m a graphic designer by trade so to me I was halfway there already: get some supplies, create some screens and make it happen! OK, so it’s definitely not that straightforward and to be honest with you, I could spend some very entertaining minutes telling you about my experience with “YouTube versus reality” but instead, I’m just going to say there is a reason why screen printing is an actual profession!

So long story short though, I did do it. I gave myself a crash course in self-taught screen printing and fast forward a bit, I now design and print my own fabrics, which I turn into beautiful nursing pillows for mums who love the handmade revolution as much as I do!
So how does the process work?
This is just a basic run down, because there’s a lot of work that makes up this part. Initially I start with a basic idea and then from there I’ll draw up a few images, and once I’ve got enough to work from, I’ll refine them using Illustrator or Photoshop. It’s those refined drawings that I then use to create a seamless pattern, and it’s this pattern that goes on to be made into a silk screen.
Screen printing on larger pieces of cloth does require a bit of room, so I’ve actually commandeered over a third of our shed which has been converted into a multi-space studio for me. On one side I have my purpose-built design and sewing area – this is a strictly no paint zone – and on the other side I have my cutting table and screen printing set up. Believe it or not, early on this was actually done inside our house, but thankfully with my extended space, I’ve long since moved away from clamping homemade silk screens to our dining room table.
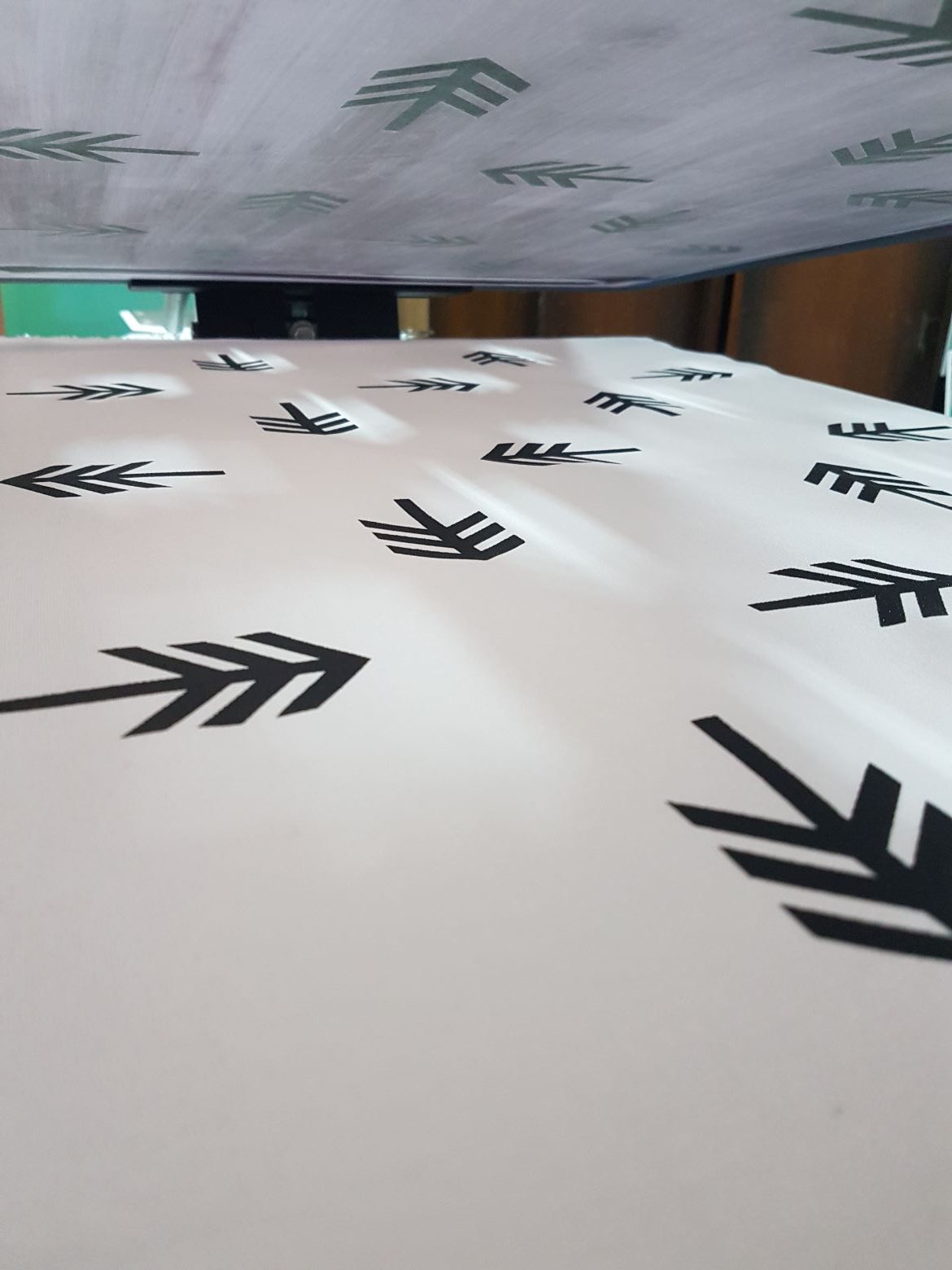
Heading back to the printing process, I’ve invested in a printing press, which was a complete game changer for me. What I do now is place my pre-cut piece of fabric or base cloth over my press with the screen I need locked in place above it, then I’ll apply a water base ink to the screen, and with a very large squeegee I’ll work it through onto the fabric. This technique itself does actually require a great deal of skill, especially because of the large surface area I’m printing on. If I’m too heavy handed during this process or not heavy handed enough, the result will either be a flooded image or not enough image at all, so it’s all about getting the right pressure and the right rhythm going.